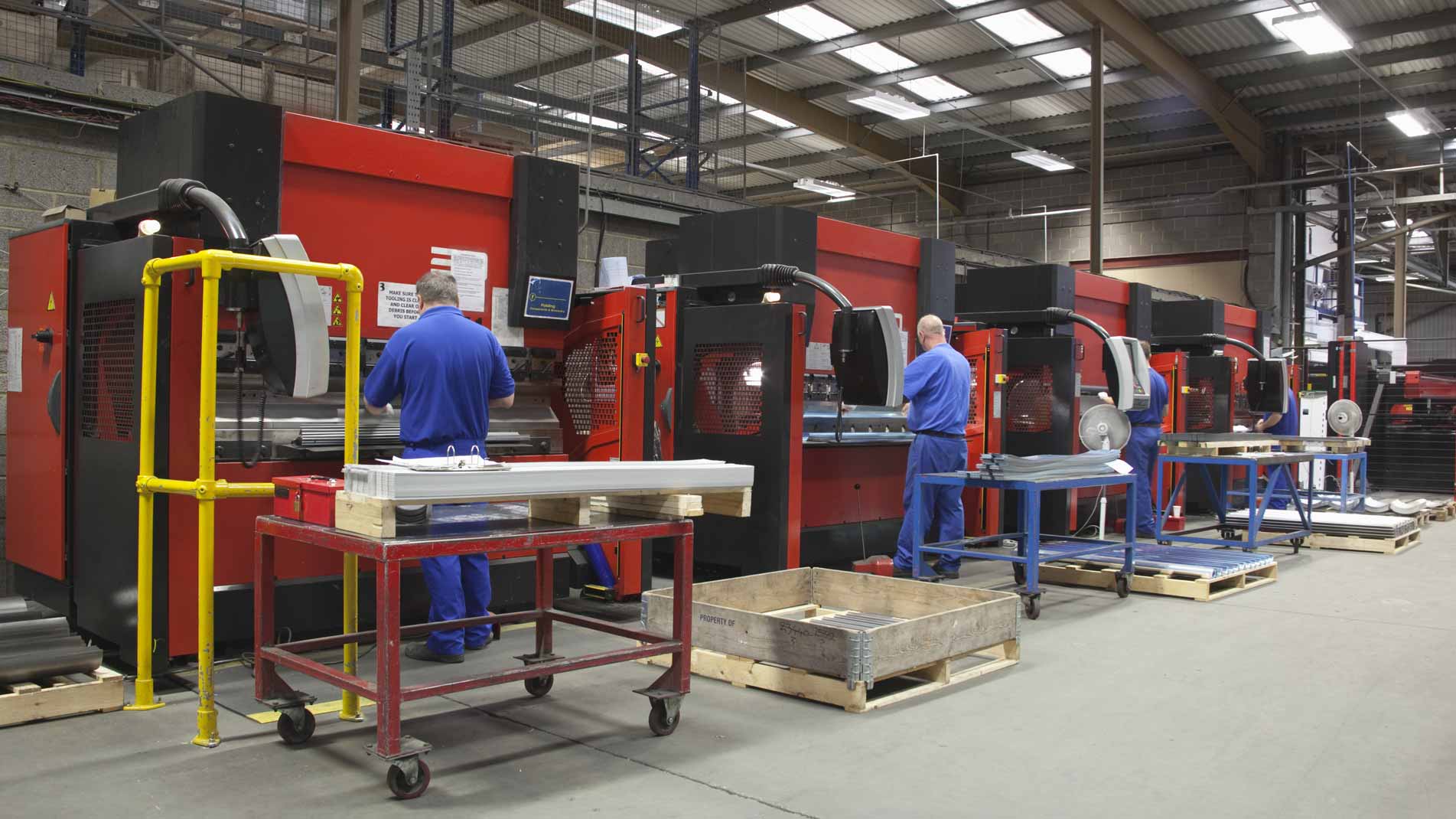
WMS for Manufacturing
Effective integration of supply processes in manufacturing lines with finished product stored away
Ask Our ExpertsReal-time stock visibility and tracking of raw materials and semi-finished or finished products
Manufacturing processes can play a key part in getting the most out of your supply chain and are one of the biggest challenges in doing business.
Our WMS for Manufacturing gives you access to specific tools that provide efficiency and tracking throughout this process.
Benefits
- Visible stock management, all in real-time.
- Just-in-time manufacturing support.
- Oversee your items master and Bill of Materials (BOM).
- Improve runtimes in manufacturing processes.
- Better quality products.
- Easy tracking, genealogy and regulatory compliance.
- Go paperless: online interface via RF devices and touch-screen displays.
How the WMS for Manufacturing software works
-
Manage Bills of Materials (BOM). Manufacture orders are created based on this information. Here, raw materials are configured in order to make finished or manufactured products.
Managing the materials list can be done from an ERP or, manually, from the user interface of the manufacturing module.
It is possible to set a minimum amount of finished product to be made. In the event there is not enough raw material to manufacture the required quantity, the manufacture order will not be completed.
Additives, such as raw materials, can also be entered. In other words, these items are not usually supplied or kept in stock, but are registered the moment they are used to manufacture items.
-
Configure manufacturing lines. The place where the manufacturing process is carried out. Different manufacturing lines may share supply buffers or finished product staging areas.
A manufacturing line is a workstation setup with:
- Supply buffer: a staging area where raw material stock is taken that is needed for a BOM to be manufactured.
- Manufacturing buffer: a staging area where finished product is created as a result of the manufacturing process.
-
Management of manufacture orders. A raw material processing order for finished products in a manufacturing line drawn from a BOM. Manage everything through the ERP or the software user interface of the WMS for Manufacturing.
The release of a manufacture order involves the creation of a raw material supply order that is sent to the supply buffer area, following this procedure:
- Launch of a manufacture order to a manufacturing line
- Raw materials supplied to the manufacturing line
- Raw materials consumed in the line
- Creation of the finished product
- Closure of the manufacture order
-
Management of supply orders for the manufacturing line. Warehouse exit orders are sent to the line’s supply buffer with the raw material stock needed for a manufacture order.
The supply orders are created when the manufacture order is released.
Easy WMS allocates the raw material required to make the finished product and creates and oversees the picking tasks the operators must do to bring these raw materials to the supply buffer.
Before launching the supply order, the system verifies that the warehouse has enough stock to fulfil the specified minimum amount on the materials list.
-
Manual consumption of raw material. An operator with a radiofrequency device or hand-held tablet indicates the raw material that has been inserted into the manufacturing line.
This type of consumption is useful when the supply buffer, due to capacity issues, cannot hold all necessary raw material at once to produce everything listed on the manufacture order.
As raw material is consumed, space is freed up in the supply buffer and Easy WMS can then keep extracting more raw materials from the warehouse.
-
Automatic consumption of raw material. The consumption of raw materials happens during the making of finished products.
Raw materials are consumed in proportion to the amounts listed on the BOM. In other words, it involves notional consumption that could be fine-tuned later on.
Stock that is considered as consumed is selected via FEFO (first expires, first out) criterion.
This type of consumption is useful when:
- The supply buffer has all necessary raw materials to manufacture everything shown on the manufacture order.
- There is no need to free up space in the manufacturing buffer in order to keep supplying it with raw materials, either because operators make finished products very quickly or because the manufacturing process within the line is sufficiently slow-moving.
-
Making finished products. Using a RF device, workers register the stock produced, specifying the containers these have been introduced into.
The finished products are made from the stock consumed on the manufacturing lines.
When making finished product, it is possible to keep track of whether the produced stock is defective and, as such, is unfit for use or sale. Raw materials are still listed as consumed, although this faulty stock does appear in the system.
-
Exact/inexact tracking. Consumed stock can come from different batches, meaning finished products could contain raw material from any of these, without being able to pinpoint which one it came from exactly. The WMS for Manufacturing software stores all batches of raw material that could be used to manufacture finished product.
When a quality issue is detected in a certain batch of raw material, the WMS for Manufacturing software can determine all the finished product made from this raw material.
-
Closure of a manufacture order. These must reflect changes made in the consumption of raw materials and the creation of finished product.
Once the creation of finished product is completed, an operator must close the manufacture order via an RF device or from a PC or tablet.
The operator must enter the following information:
- Adjust the actual raw material consumed in the event this does not match the usage calculated on the BOM.
- Adjust the amount of finished product in the event this also does not match those calculated on the BOM.
- Specify any damage to raw materials.
- Specify any defective finished product.
- Specify the consumption of additives.
The WMS for Manufacturing software keeps your ERP up-to-date with the data gathered by operators.
-
Manufacture report. Creation of a report containing the data of the manufacture order, the stock made, the raw materials used and the stock consumed.